Predictive Maintenance: Vorteile der Instandhaltung der Zukunft
Im Zeitalter der digitalen Transformation hat sich Predictive Maintenance als wegweisende Strategie für die Anlagenwartung etabliert. Diese innovative Herangehensweise revolutioniert die traditionellen Instandhaltungsmethoden und passt sie an die Anforderungen der modernen Industrielandschaft an.
Predictive Maintenance nutzt die Synergien aus fortschrittlicher Sensorik, umfangreichen Datenanalysen und künstlicher Intelligenz, um potenzielle Maschinenausfälle frühzeitig zu erkennen. Dadurch können Unternehmen ihre Wartungsabläufe optimieren und Stillstandzeiten minimieren.
Dieser Artikel bietet einen umfassenden Einblick über Predictive Maintenance. Wir beleuchten die Grundlagen, Funktionsprinzipien und Vorzüge dieser Technologie sowie ihre vielfältigen Einsatzmöglichkeiten in verschiedenen Industriezweigen.
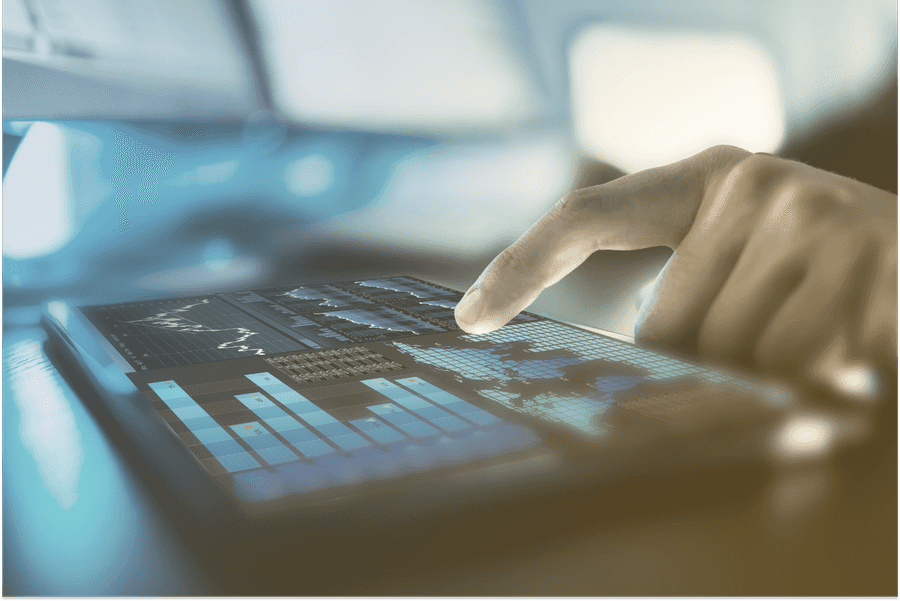
Was ist Predictive Maintenance?
Predictive Maintenance, auch als vorausschauende Instandhaltung bekannt, ist ein innovativer Ansatz zur Wartung von Maschinen und Anlagen. Im Gegensatz zu herkömmlichen Wartungsmethoden basiert Predictive Maintenance auf der kontinuierlichen Überwachung und Analyse von Maschinendaten, um potenzielle Ausfälle frühzeitig zu erkennen und zu verhindern.
Der Kern von Predictive Maintenance liegt in der Nutzung von Sensoren, die verschiedene Parameter wie Temperatur, Vibration oder Druck in Echtzeit erfassen. Diese Daten werden mithilfe fortschrittlicher Algorithmen und Verfahren des maschinellen Lernens analysiert, um Muster zu erkennen und Prognosen über den Zustand der Maschine zu erstellen.
Das Ziel von Predictive Maintenance ist es, Wartungsarbeiten genau dann durchzuführen, wenn sie tatsächlich erforderlich sind - nicht zu früh und nicht zu spät. Dadurch werden ungeplante Ausfälle vermieden, die Lebensdauer der Anlagen verlängert und die Effizienz der Wartungsprozesse erhöht.
Wie funktioniert Predictive Maintenance?
Die Funktionsweise von Predictive Maintenance lässt sich in mehrere Schritte unterteilen:
- Datenerfassung: Sensoren an den Maschinen und Anlagen erfassen kontinuierlich relevante Daten wie Temperatur, Vibration, Druck oder Stromverbrauch.
- Datenübertragung: Die gesammelten Daten werden über das Internet of Things (IoT) an ein zentrales System in der Cloud übertragen.
- Datenanalyse: Mithilfe von Big Data-Technologien und Algorithmen des maschinellen Lernens werden die Daten analysiert, um Muster und Anomalien zu erkennen.
- Prognose: Basierend auf den Analyseergebnissen werden Vorhersagen über den zukünftigen Zustand der Maschine getroffen und mögliche Ausfälle prognostiziert.
- Handlungsempfehlung: Das System gibt Empfehlungen für notwendige Wartungsmaßnahmen und den optimalen Zeitpunkt für deren Durchführung.
Durch diesen Prozess können Unternehmen Wartungsarbeiten besser planen, Ersatzteile rechtzeitig beschaffen und Ausfallzeiten minimieren. Die kontinuierliche Überwachung ermöglicht es zudem, die Datenbasis stetig zu erweitern und die Prognosen immer präziser zu machen.
Predictive Maintenance vs. Condition Monitoring: Was ist der Unterschied?
Obwohl Predictive Maintenance und Condition Monitoring oft in einem Atemzug genannt werden, gibt es wichtige Unterschiede zwischen diesen beiden Ansätzen:
Condition Monitoring konzentriert sich auf die kontinuierliche Überwachung des aktuellen Zustands einer Maschine oder Anlage. Es erfasst und analysiert Daten in Echtzeit, um Abweichungen vom Normalzustand zu erkennen. Condition Monitoring kann als Grundlage für Predictive Maintenance dienen, geht aber nicht so weit, Vorhersagen über zukünftige Ausfälle zu treffen.
Predictive Maintenance hingegen nutzt die durch Condition Monitoring erfassten Daten, um mithilfe fortschrittlicher Analysemethoden und künstlicher Intelligenz Prognosen über den zukünftigen Zustand der Maschine zu erstellen. Es geht also einen Schritt weiter und ermöglicht eine vorausschauende Planung von Wartungsarbeiten.
Während Condition Monitoring eine reaktive Herangehensweise darstellt, bei der auf erkannte Probleme reagiert wird, ist Predictive Maintenance proaktiv und zielt darauf ab, Probleme zu antizipieren, bevor sie auftreten.
Welche Vorteile bietet Predictive Maintenance?
Die Implementierung von Predictive Maintenance bietet Unternehmen zahlreiche Vorteile:
- Reduzierung von Ausfallzeiten: Durch die frühzeitige Erkennung potenzieller Probleme können ungeplante Ausfälle fast vollständig vermieden werden.
- Kosteneinsparungen: Predictive Maintenance optimiert den Wartungsprozess, reduziert unnötige Wartungsarbeiten und verlängert die Lebensdauer von Maschinen und Ersatzteilen.
- Erhöhte Effizienz: Die vorausschauende Planung von Wartungsarbeiten ermöglicht eine bessere Ressourcenallokation und steigert die Produktivität.
- Verbesserte Sicherheit: Durch die frühzeitige Erkennung von Verschleiß und potenziellen Ausfällen werden Sicherheitsrisiken minimiert.
- Optimierte Ersatzteilhaltung: Die präzisen Vorhersagen ermöglichen eine bedarfsgerechte Lagerhaltung von Ersatzteilen.
- Datenbasierte Entscheidungsfindung: Die umfangreiche Datenanalyse liefert wertvolle Erkenntnisse für strategische Entscheidungen im Anlagenmanagement.
Diese Vorteile führen in der Summe zu einer signifikanten Steigerung der Anlageneffizienz und -verfügbarkeit sowie zu erheblichen Kosteneinsparungen.
In welchen Branchen wird Predictive Maintenance eingesetzt?
Predictive Maintenance findet in verschiedenen Branchen Anwendung, insbesondere in solchen, die stark von der Zuverlässigkeit ihrer Maschinen und Anlagen abhängig sind:
- Fertigungsindustrie: In Produktionsanlagen werden Maschinen kontinuierlich überwacht, um Stillstandzeiten zu minimieren und die Produktionseffizienz zu maximieren.
- Energiesektor: Bei Windkraftanlagen können mithilfe von Predictive Maintenance Ausfallzeiten fast vollständig vermieden werden. Sensoren überwachen kritische Komponenten wie Getriebe und Rotorblätter.
- Automobilindustrie: Sowohl in der Produktion als auch bei der Wartung von Kraftfahrzeugen spielt Predictive Maintenance eine wichtige Rolle. Mit Hilfe von Sensoren im Motor oder im Fahrwerk von Fahrzeugen können teure Reparaturen oder Ausfälle frühzeitig vermieden werden.
- Luftfahrt: In der Luftfahrtindustrie ist die Sicherheit von höchster Priorität. Predictive Maintenance hilft, kritische Komponenten zu überwachen und potenzielle Probleme frühzeitig zu erkennen.
- Schienenverkehr: Im Schienenverkehr werden Züge und Infrastruktur mithilfe von Predictive Maintenance überwacht, um Verspätungen zu reduzieren und die Sicherheit zu erhöhen.
Diese Beispiele zeigen, dass Predictive Maintenance besonders interessant für das produzierende Gewerbe und Branchen mit hohem Automatisierungsgrad ist.
Wie implementiert man Predictive Maintenance?
Die Implementierung von Predictive Maintenance erfordert einen strukturierten Ansatz:
- Bestandsaufnahme: Identifizieren Sie kritische Maschinen und Anlagen, die von Predictive Maintenance profitieren können.
- Sensorinstallation: Rüsten Sie die ausgewählten Maschinen mit geeigneten Sensoren aus, um relevante Daten zu erfassen.
- Dateninfrastruktur: Implementieren Sie eine robuste IT-Infrastruktur zur Datenübertragung, -speicherung und -verarbeitung, oft unter Nutzung von Cloud-Technologien.
- Datenanalyse: Entwickeln Sie Algorithmen und Modelle zur Analyse der erfassten Daten und zur Erstellung von Prognosen.
- Integration: Integrieren Sie das Predictive Maintenance-System in bestehende Wartungs- und Produktionsprozesse.
- Schulung: Schulen Sie das Personal im Umgang mit dem neuen System und in der Interpretation der Ergebnisse.
- Kontinuierliche Verbesserung: Überwachen und optimieren Sie das System fortlaufend, um die Genauigkeit der Prognosen zu verbessern.
Eine erfolgreiche Implementierung erfordert oft die Zusammenarbeit verschiedener Abteilungen und möglicherweise die Unterstützung externer Experten.
Welche Herausforderungen gibt es bei der Einführung von Predictive Maintenance?
Trotz der vielen Vorteile stehen Unternehmen bei der Einführung von Predictive Maintenance vor einigen Herausforderungen:
- Datenqualität und -menge: Für präzise Vorhersagen sind große Mengen qualitativ hochwertiger Daten erforderlich. Die Erfassung und Verwaltung dieser Datenmengen kann eine Herausforderung darstellen.
- Technische Komplexität: Die Implementierung von Predictive Maintenance erfordert fortschrittliche technische Kenntnisse in Bereichen wie Sensorik, Datenanalyse und maschinelles Lernen.
- Integration in bestehende Systeme: Die Einbindung von Predictive Maintenance in vorhandene IT- und Produktionssysteme kann komplex sein.
- Investitionskosten: Die anfänglichen Kosten für Sensoren, IT-Infrastruktur und Software können beträchtlich sein.
- Kultureller Wandel: Die Umstellung von reaktiver auf vorausschauende Wartung erfordert oft einen Kulturwandel im Unternehmen.
- Datensicherheit: Die Sammlung und Analyse großer Datenmengen wirft Fragen zur Datensicherheit und zum Datenschutz auf.
Um diese Herausforderungen zu bewältigen, ist eine sorgfältige Planung und schrittweise Implementierung empfehlenswert.
Welche Technologien sind für Predictive Maintenance wichtig?
Predictive Maintenance basiert auf einer Kombination verschiedener Technologien:
- Internet of Things (IoT): Vernetzung von Maschinen und Sensoren zur Datenerfassung und -übertragung.
- Sensortechnologie: Fortschrittliche Sensoren zur präzisen Erfassung verschiedener Maschinenparameter.
- Big Data: Technologien zur Verarbeitung und Analyse großer Datenmengen.
- Cloud Computing: Skalierbare Infrastruktur zur Datenspeicherung und -verarbeitung.
- Künstliche Intelligenz und maschinelles Lernen: Fortschrittliche Algorithmen zur Mustererkennung und Prognose.
- Datenvisualisierung: Tools zur anschaulichen Darstellung komplexer Daten und Prognosen.
- Mobile Technologien: Smartphones und Tablets zur Überwachung und Steuerung von Anlagen.
Die kontinuierliche Weiterentwicklung dieser Technologien treibt auch die Evolution von Predictive Maintenance voran und eröffnet neue Möglichkeiten für noch präzisere und effizientere Wartungsstrategien.
Fazit: Ist Predictive Maintenance der Schlüssel zur effizienten Instandhaltung?
Predictive Maintenance revolutioniert die industrielle Instandhaltung durch präzise Vorhersagen von Wartungsbedarf und potenziellen Ausfällen. Die Vorteile sind beeindruckend: reduzierte Ausfallzeiten, optimierte Kosten und verlängerte Maschinenlebensdauer. Obwohl die Implementierung Herausforderungen mit sich bringt, wird Predictive Maintenance zunehmend zum Standard in der Industrie 4.0.
Unternehmen, die frühzeitig auf diese Technologie setzen, können sich einen bedeutenden Wettbewerbsvorteil sichern. Predictive Maintenance ist nicht nur ein Trend, sondern ein essenzieller Baustein für eine effiziente, zukunftsorientierte Instandhaltung.
Möchten Sie mehr darüber erfahren, wie Predictive Maintenance Ihr Unternehmen voranbringen kann? Zögern Sie nicht, uns zu kontaktieren! Das Expertenteam von DevDuck steht bereit, um Ihre spezifischen Anforderungen zu analysieren und maßgeschneiderte Lösungen für Ihre Instandhaltungsprozesse zu entwickeln.